Superalloys
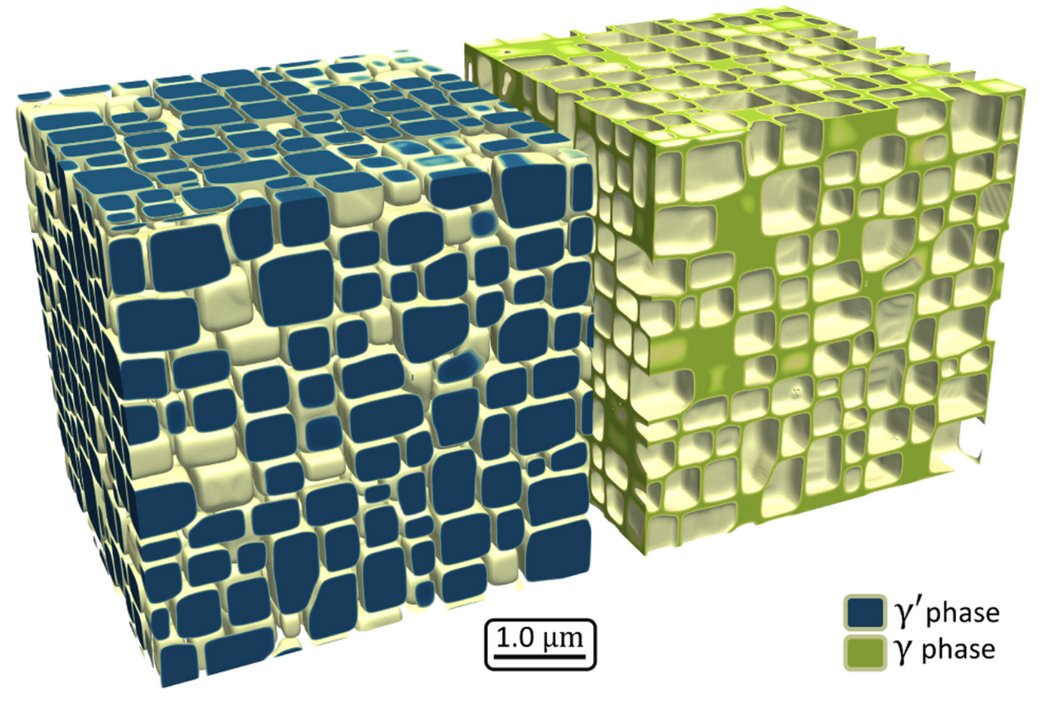
References
Introduction
Single crystal nickel-based superalloy blades are crucial components of high-temperature engine turbines and aero turbines owing to their top-notch mechanical performance and extreme heat resistance. Superior creep and fatigue performance in Ni-based superalloys relies mostly on the microstructure, where a substantial volume fraction of ordered precipitates resides in the matrix.
Gamma prime precipitate exhibit a smaller lattice constant, which produce compression and tension in the gamma matrix and precipitate, respectively. External stress and high temperature cause the precipices to evolve in a directed fashion. The direction of evolution of precipitates is determined by the sign of external stress, misfit, and anisotropy of gamma and gamma prime.
Simulation setup
The OpenPhase® built-in example, "Superalloys" is used to model the evolution of gamma prime in the super-saturated gamma matrix. Interfacial, chemical, and mechanical free energy contributions are included.
Strain gradient crystal plasticity model is employed [1]. Ni-Al binary alloy is employed with the modified diffusion coefficient of the "Re". Mechanical driving force aids in the formation of cuboidal precipitates. The table includes all the simulation parameters [2].
Quasi-random Nuclei function is employed from the Initialization class and allow them grow. Having anisotropic elastic constant enables them to develop cubic shape with the volume fraction of 65%.
Results
Fig. 1 represents the initial microstructure of Ni-based superalloys after the fully developed gamma prime precipitates which have been used for the creep test. There are 500 particles with an average size of 450 nm and a channel width of 60 nm. The wetting condition is imposed by increasing the interfacial energy σγ′-γ′ three times greater than σγ-γ′ which prevents gamma prime from merging.
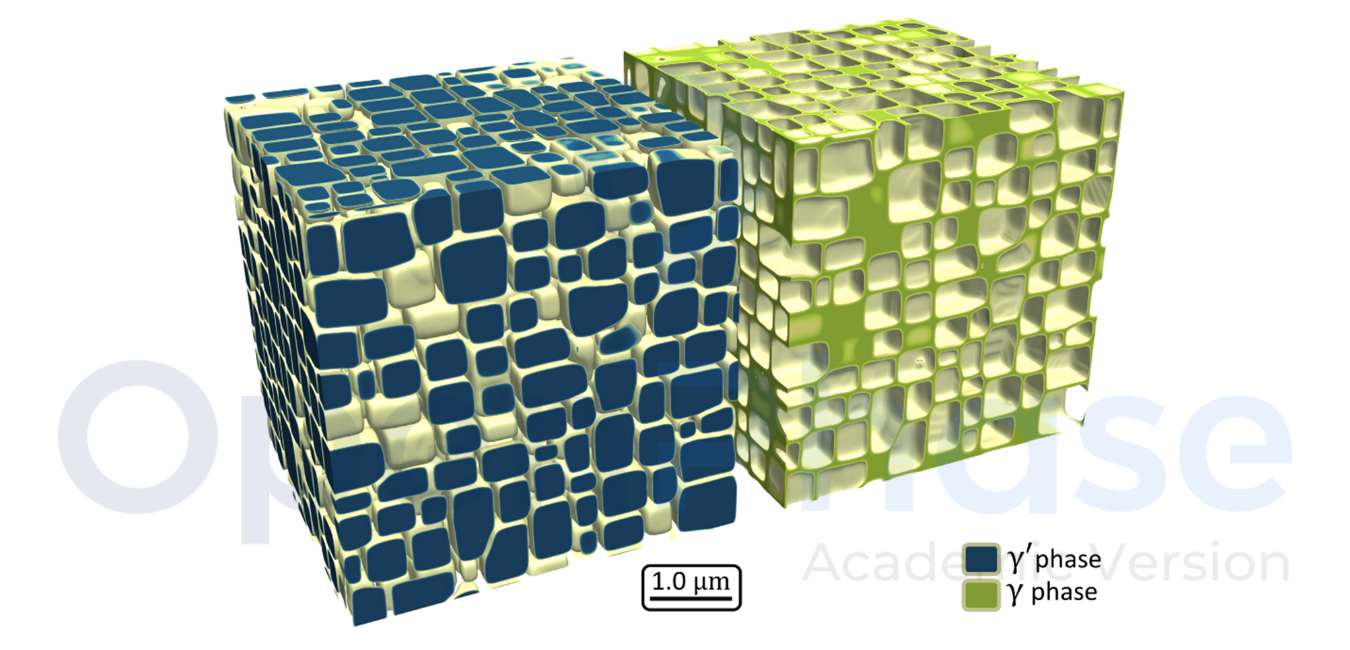
Figure 1: Initial Ni-based superalloys microstructure with the volume fraction of gamma prime is 65%.
The system is subjected to a constant tensile stress of 350 MPa at the temperature of 900°C along the [001] cubic axis. The density of dislocations is confined to the gamma matrix and pushed away with a moving interface. Tensile stress causes greater stress in the channels perpendicular to the applied direction, whereas compressive stress causes greater stress in the channels parallel to the applied direction. When the interfacial dislocation reaches a critical value, the wetting condition is removed, permitting the overlapping precipitates to coalesce.
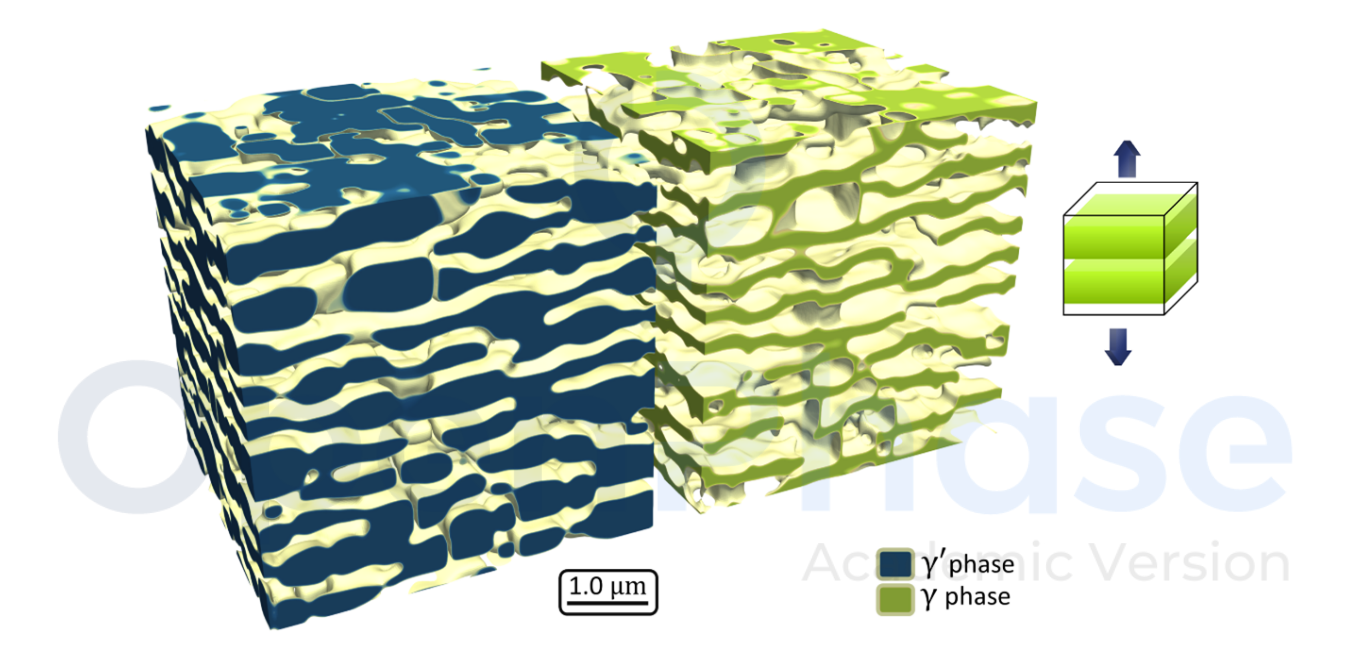
Figure 2: Evolved microstructure at 1% creep strain after applied tensile stress.
Fig. 2 depicts the microstructure at 1% creep strain under tensile stress. Rafting is carried out perpendicular to the applied stress. Coalescence occurs because of the coherency loss determined by the dislocation density [3]. The rafted microstructure in compression is depicted in Fig. 3. The rafting occurs at the perpendicular of the applied stress.
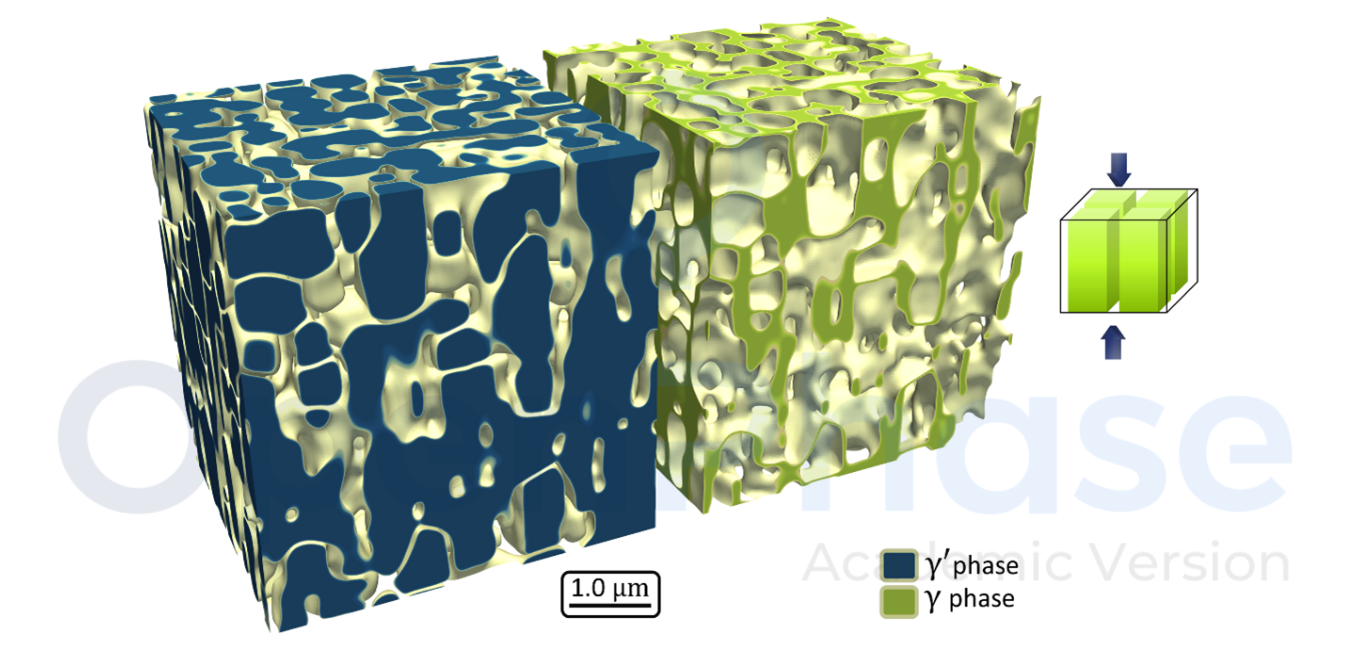
Figure 3: Evolved microstructure at 1% creep strain after applied compressive stress.
Related Topics
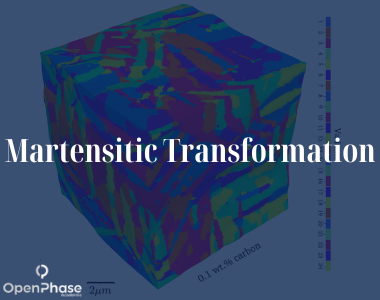
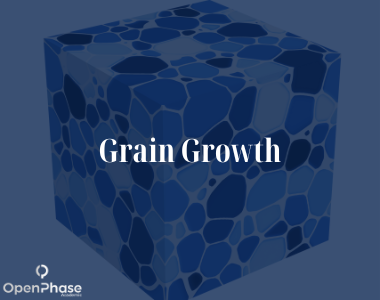
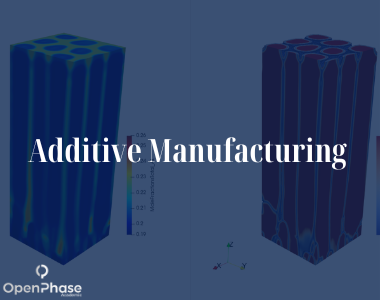