Reactive Gas Flows in Granular Particle Assemblies
References
Introduction
Flow of reactive gases is a ubiquitous phenomenon encountered both in everyday life and in industrial processes, e.g., burning of natural gas in domestic heating and cooking as well as in large scale energy plants. There are also applications, where the gas is not the only combustible component but serves to ignite and accompany the combustion of solid particles. In all these cases, it is of major economic and environmental interest to optimize the system and process parameters such that the maximum possible energy is gained per unit mass of the combustible material. To achieve this goal, a hybrid simulation methodology has been developed which allows to study reactive gas flows through assemblies of solid particles/particle beds [1]. The new modules combine the lattice Boltzmann (LB) method, the finite difference (FD) scheme and the phase-field (PF) approach into a monolithic framework in a massively parallel high performance computing environment.
Result
To validate the code, the above mentioned LB-FD-PF methodology has been used to study a one-dimensional flame. In this case, a reactive gas (fuel) enters the channel with a prescribed velocity and is ignited roughly in the middle of the channel. The flame front moves towards the inlet, if the flow velocity is lower than the flame velocity. In the opposite case of high gas velocity, it moves towards the outlet. As expected a steady immobile flame is established in numerical simulations if the flow velocity agrees with the estimate for the flame velocity (Fig. 1).
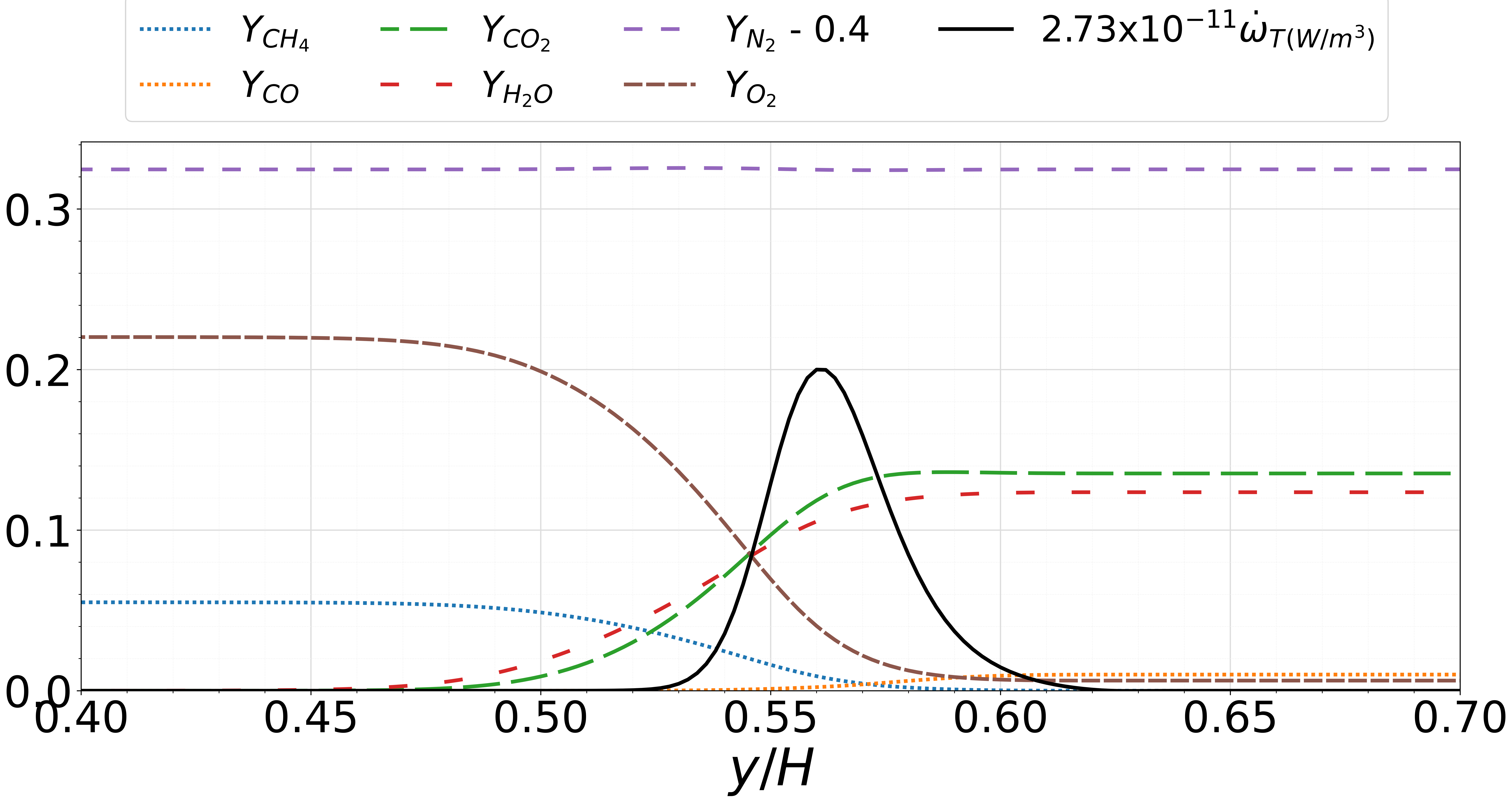
Figure 1: Mass fractions of the species participating in the 1-D flame of methane/air mixture. For visibility, the N2-mass fraction is shifted downwards and the heat production rate is multiplied by a constant number [2].
This new simulation scheme is then used to study a flame in a channel made of two parallel solid walls with a wall-to-wall distance H. These simulations serve to study the temperature distribution and flame structure. The velocity profile at the inlet is set to be parabolic along the transverse direction but independent of the longitudinal coordinate. To establish a flame at a distance H/4 from the inlet, the first quarter of the domain is filled with a fresh methane/air mixture at T=300K and the remaining portion of the domain is filled with post-combustion fluids at T=2200K. At the beginning of simulations, pressure waves occur which can disrupt the stabilization process. This problem becomes more pronounced in the presence of a flame. The use of a non-reflecting pressure outlet boundary condition helps to effectively damp these undesired reflections and thus avoid the related numerical instabilities. The parameters and conditions used in these simulations are reported in Tabel 1.
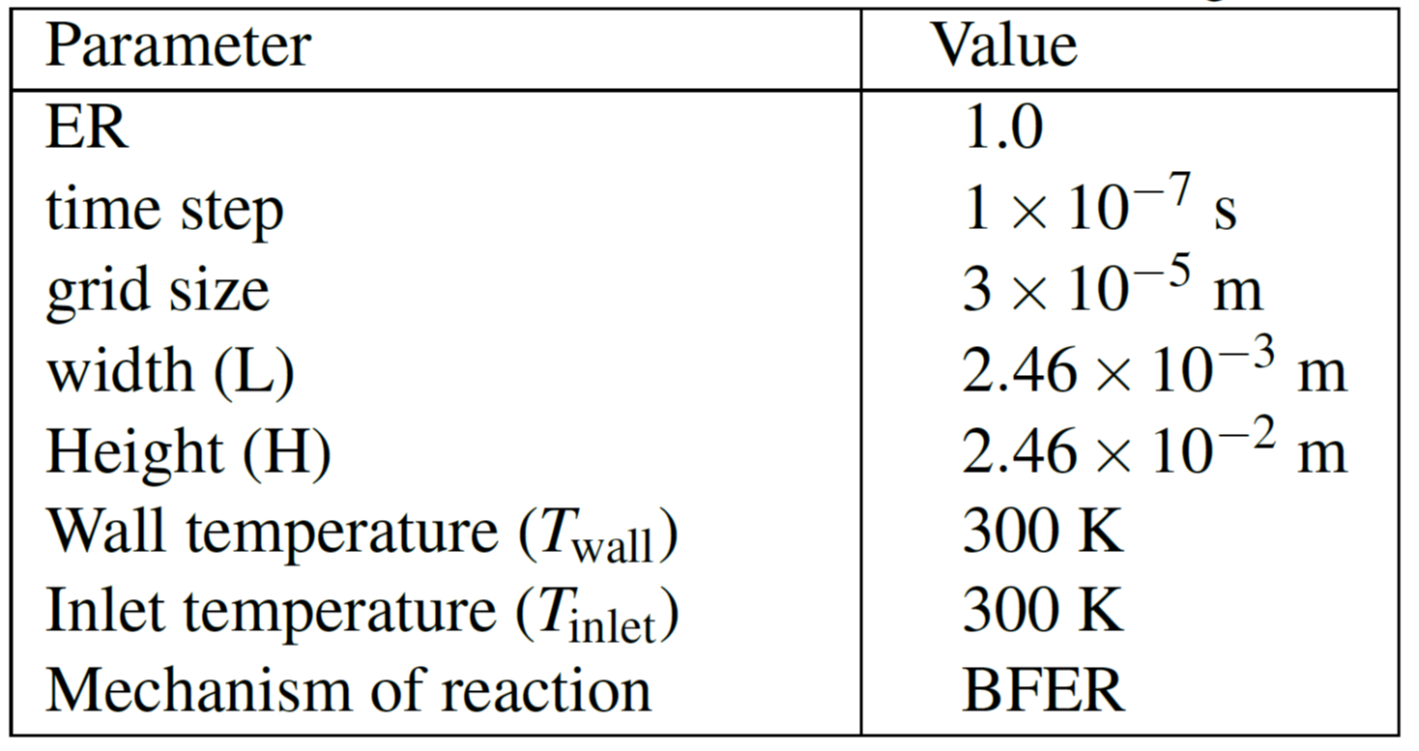
Table 1: Parameters used in the simulations of the 2D-flame, whose results are shown in Fig.2.
The code has been also used to simulate a flame in a methane/air mixture flowing through a regular array of cylinders. Results obtained from these studies agree well with experiments [2] and also with numerical simulations using an alternative software, ALBORZ [3].
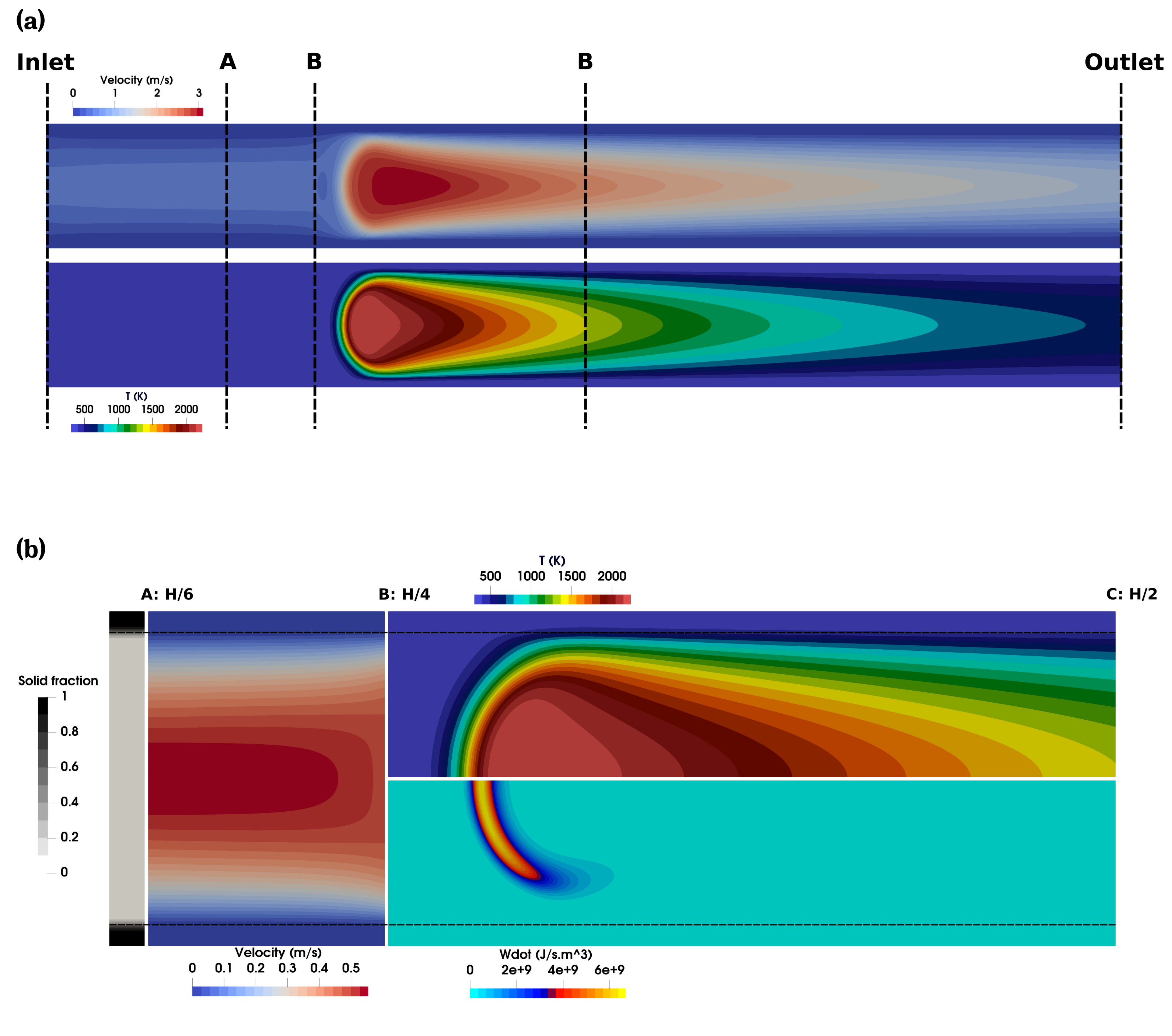
Figure 2: (a) The velocity and temperature distributions within a 2-D simulation of a flame confined between two parallel walls. The temperature is kept constant at 300 K for both the walls and for the fluid at the inlet. (b) A closer view of the flame front, where substantial gradients in both velocity and temperature fields occur. The upper half shows the temperature field and the lower one highlights the flame structure.
Related Topics
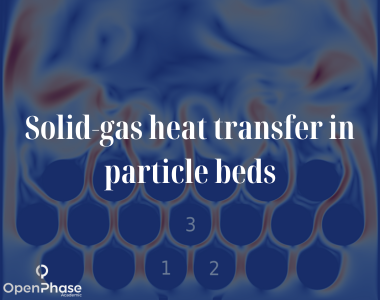
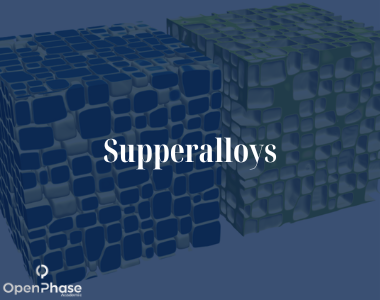
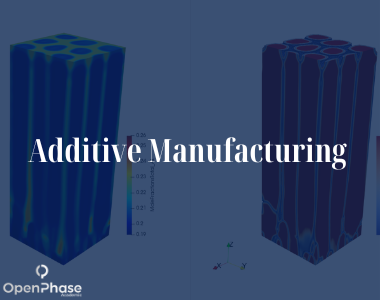